Korozja jest jedną z przyczyn największych strat ekonomicznych na świecie. Szacuje się, że korozja doprowadza do zniszczenia nawet 25 mln ton stali. Straty ekonomiczne obejmują zarówno koszt zniszczonych materiałów, konstrukcji, jak i koszty związane z naprawą tych konstrukcji i ich ochroną przed skutkami korozji. Poza stratami bezpośrednimi, korozja powoduje także straty pośrednie, związane z narażeniem zdrowia lub życia ludzkiego, a także środowiska. Dlatego tak istotne jest zapewnienie odpowiedniej ochrony antykorozyjnej, która skutecznie ochroni stalowe konstrukcje, a także metalowe elementy. Rodzaj zabezpieczenia antykorozyjnego powinien być dopasowany do specyfiki środowiska w jakim znajduje się dana konstrukcja oraz wystawienia na czynniki zewnętrzne.
Jako producent konstrukcji stalowych o różnym zastosowaniu, doskonale wiemy, jakie ryzyko niesie ze sobą korozja. Dla przemysłu, infrastruktury miejskiej, transportowej czy energetycznej, korozja może oznaczać zniszczenia przekładające się na duże straty finansowe. Aby tego uniknąć, warto zdecydować się na zabezpieczenie antykorozyjne – szczególnie w przypadku konstrukcji przemysłowych w agresywnym środowisku, a także w warunkach zewnętrznych. W tym artykule przeanalizujemy najlepsze dostępne zabezpieczenia antykorozyjne – ich zalety i słabe punkty, a także ich zastosowanie w różnych branżach.
Czym jest korozja i jakie są jej skutki?
Korozja jest naturalnym procesem chemicznym lub elektrochemicznym, który prowadzi do stopniowego niszczenia metali na skutek ich reakcji ze środowiskiem. Najczęściej spotykaną formą korozji jest rdzewienie żelaza i stali, które zachodzi pod wpływem kontaktu metalu z tlenem i wilgocią – tworzy się wówczas tlenek żelaza, potocznie nazywany rdzą. Proces korodowania może mieć różne formy i przebiegać z różną intensywnością. Wpływ na to mają różne czynniki, m.in.:
- rodzaju metalu,
- warunki atmosferyczne (wilgotność, temperatura, dostęp do tlenu),
- obecności związków chemicznych (szczególnie w środowiskach przemysłowych),
- czasu ekspozycji na negatywne czynniki
Korozja może mieć różne formy, co wiąże się także z jej specyfiką. Wyróżniamy m.in. korozję równomierną, która obejmuje całą powierzchnię metalu w sposób jednolity. Ten rodzaj korozji jest najczęściej bardzo powierzchniowy, jednak obejmuje bardzo rozległe obszary. Innym typem zniszczeń spowodowanych przez rdzę są wżery, czyli pojawiające się punktowo, ale bardzo głębokie zmiany spowodowane korozją. Mogą mieć one kluczowy wpływ na trwałość konstrukcji, choć z pozoru wydają się niewielkie.
Wyróżniamy jeszcze korozję międzykrystaliczną, która rozwija się na granicach ziaren struktury metalu, często niezauważalna gołym okiem. Z korozją elektrochemiczną mamy ty czynienia, gdy dwa różne metale stykają się w obecności elektrolitu (np. wody zawierającej sól).
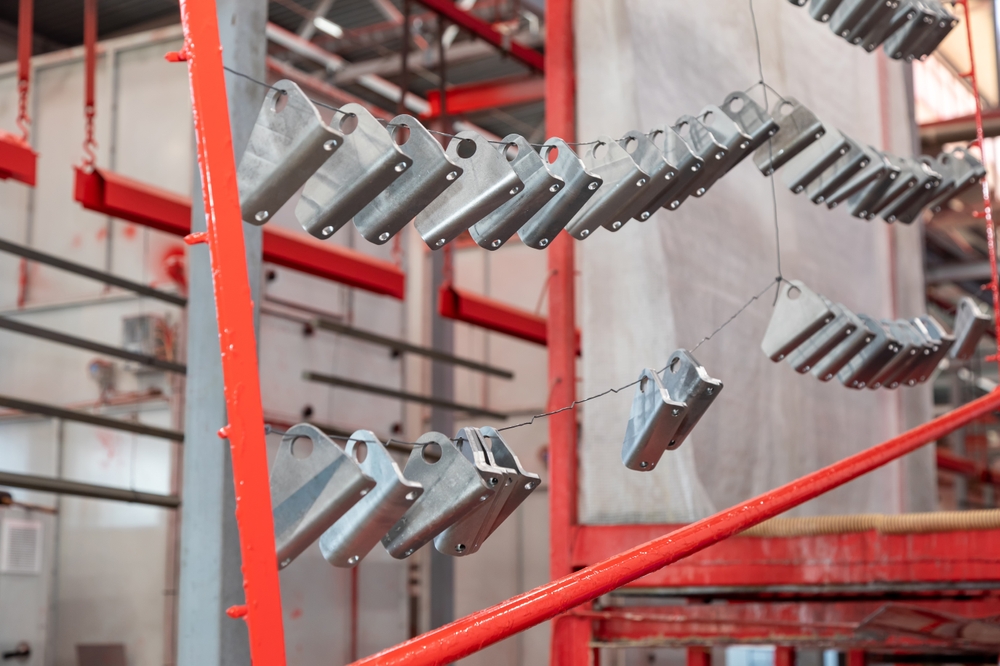
Działania antykorozyjne – jak zminimalizować działanie negatywnych czynników?
W celu zmniejszenia skutków korozji, należy już na początku pomyśleć o zastosowaniu odpowiedniego zabezpieczenia antykorozyjnego. Wybór właściwej ochrony przeciw korozją pozwoli zabezpieczyć powierzchnię metalu przed działaniem czynników zewnętrznych – wody, wilgoci, wody morskiej, czy substancji chemicznych, które mogłyby powodować niszczenie. Zabezpieczenie przeciw korozją najczęściej polega na wykonaniu trwałej powłoki, która ma za zadanie stworzyć swojego rodzaju „płaszcz” oddzielający metalową powierzchnię od czynników zewnętrznych.
Aktualnie stosuje się kilka różnych rodzajów zabezpieczeń antykorozyjnych. Dzięki temu możliwe jest dopasowanie najlepszej metody do danego zastosowania i warunków. Jedną z najczęściej stosowanych metod zabezpieczenia antykorozyjnego metalu jest nakładanie powłok ochronnych w postaci specjalnej farby. Do najpopularniejszych technik należą malowanie proszkowe i malowanie hydrodynamiczne.
Malowanie proszkowe metalu dla ochrony przed korozją
Malowanie proszkowe to nowoczesna technika, polegająca na nanoszeniu farby w postaci proszku na naelektryzowaną powierzchnię metalu. Następnie element trafia do pieca, gdzie w wysokiej temperaturze (ok. 160–200°C) farba ulega stopieniu i utwardzeniu, tworząc gładką, trwałą i estetyczną powłokę. Najczęstsze zastosowanie to ogrodzenia, balustrady, profile aluminiowe, elementy motoryzacyjne, części maszyn.
Jakie są zalety malowania proszkowego?
- bardzo wysoka odporność na korozję, promieniowanie UV, uszkodzenia mechaniczne i chemiczne,
- możliwość uzyskania różnorodnych wykończeń: mat, półmat, połysk, szeroka kolorystyka,
- równomierne pokrycie nawet trudno dostępnych miejsc.
Należy jednak pamiętać, że piaskowanie wymaga odpowiedniego przygotowania powierzchni. Metoda ta ma także ograniczenia w rozmiarze elementów – musi zmieścić się do pieca.
Malowanie hydrodynamiczne
Malowanie hydrodynamiczne, zwane też natryskiem bezpowietrznym, to technika, w której farba jest rozpylana pod bardzo wysokim ciśnieniem przez specjalny agregat malarski. W odróżnieniu od klasycznego malowania natryskowego, w tej metodzie nie używa się powietrza do rozpylania farby, co pozwala na uzyskanie jednolitej, grubej i gładkiej powłoki przy minimalnym rozprysku.
Dlaczego warto zdecydować się na malowanie hydrodynamiczne?
- szybkie tempo pracy i wysoka wydajność – idealne do dużych powierzchni,
- dobra przyczepność i równomierne pokrycie,
- możliwość nakładania różnych typów farb
- skuteczne w ochronie konstrukcji stalowych i przemysłowych.
Malowanie hydrodynamiczne znajduje zastosowanie w ochronie antykorozyjnej takich konstrukcji jak: mosty, hale przemysłowe, kontenery, konstrukcje stalowe, zbiorniki, rurociągi, maszyny rolnicze.
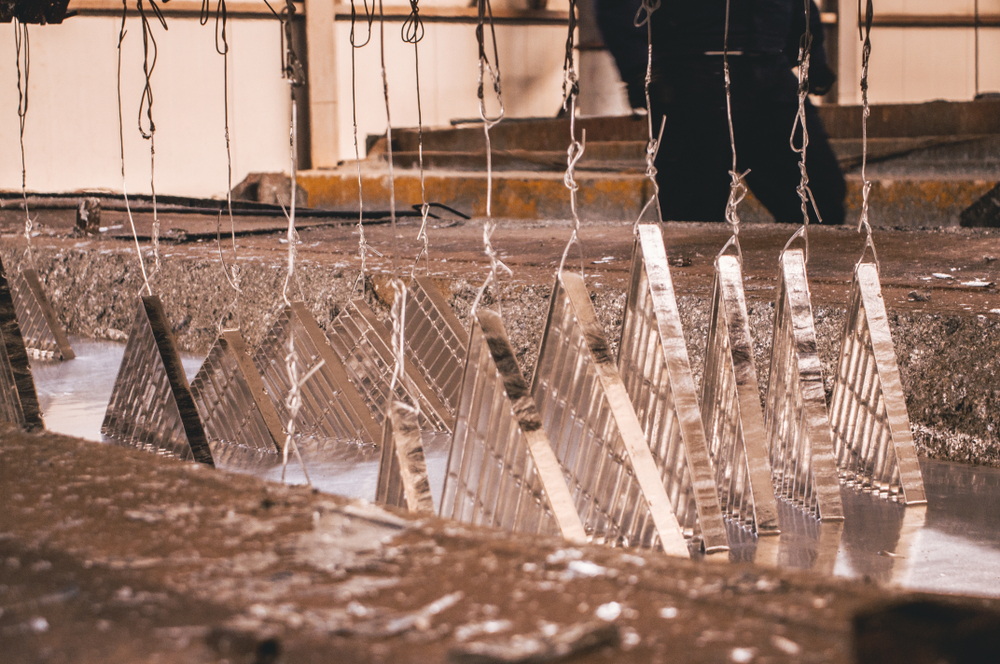
Skuteczne zabezpieczeni antykorozyjne – cynkowanie ogniowe
Cynkowanie ogniowe, zwane także cynkowaniem metodą zanurzeniową, to jedna z najskuteczniejszych metod zabezpieczania stali przed korozją. Polega na zanurzeniu wcześniej oczyszczonego elementu stalowego w ciekłym cynku o temperaturze około 450°C. W wyniku reakcji chemicznej między stalą a cynkiem powstaje trwała warstwa stopów żelazo-cynk oraz zewnętrzna powłoka czystego cynku. Metoda ta jest wybierana ze względu na jej liczne zalety:
- równomierne pokrycie elementów, nawet w trudnodostępnych miejscach i załamaniach konstrukcji,
- zabezpiecza przed uszkodzeniami mechanicznymi, ale także przed korozją elektrochemiczną,
- chroni powierzchnię metalu przed czynnikami atmosferycznymi – kwaśnymi deszczami czy mgłą solną,
- duża trwałość powłoki – nawet do kilkudziesięciu lat, bez konieczności odnawiania.
Korozja nie tylko obniża estetykę, ale również znacząco osłabia strukturę materiału, prowadząc z czasem do jego całkowitej degradacji. W skrajnych przypadkach może to prowadzić do poważnych awarii, np. w konstrukcjach stalowych, zbiornikach, rurociągach czy pojazdach. Pierwsze skutki korozji można zniwelować odpowiednimi preparatami. Jednak rozwinięta korozja skutkuje nie tylko stratami finansowymi – np. koniecznością wymiany skorodowanego elementu, zaawansowanej naprawy, lub wręcz wykonania nowej konstrukcji, ale także zwiększa niebezpieczeństwo użytkowania takich obiektów. Dlatego zapobieganie korozji poprzez odpowiednie zabezpieczenie powierzchni metalowych jest jednym z najważniejszych elementów w utrzymaniu infrastruktury i urządzeń technicznych w dobrym stanie technicznym.